Thoughts from the Diary of a Gandhian
On the occasion of 147th birth anniversary of Mahatma Gandhi, here we publish an article titled ‘Khadi as Symbol of Swaraj: Thoughts from the Diary of a Gandhian’ by T. R. Dwarakanath of Srirampura 2nd Stage, Mysuru, highlighting how Khadi had shot to importance and was a means of livelihood in the run-up to freedom, from the diary notes of this correspondent’s father late T. K. Ramakrishna
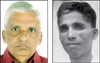
by T. R. Dwarakanath
In the second and final article as a sequel to ‘Badanavalu Movement: A Nostalgic Perspective’ (SOM dated May 17, 2015), I wish to share with the esteemed readers some of the thoughts captured as diary notes in 1946 by my father late T. K. Ramakrishna, who was the Manager of Badanavalu Spinning Circle between 1957-61. The 70-year-old manuscript (see photo) throws light on the connotations attached to khadi as symbol of Swaraj that Gandhiji championed in the run up to freedom. It also gives a kaleidoscopic view of life and times in a world that was grappling with the fallout of the Second World War.
The central role of khadi in the lives of people just before independence is indeed noteworthy. To quote from Nehru’s An Autobiography (pp. 61, Allied Publications) “… (The British) Government had decided to crush the movement. Hand-spinning on the charaka was then spreading among the peasantry at the instance of the Congress. A charaka therefore became the symbol of sedition and its owner got into trouble, the charaka itself being often burnt….” It is commemorative and significant that we are revisiting sustainable means of livelihood through the Badanavalu movement spearheaded by Prasanna and other social activists. The English translation of the article follows:
Khadi for forty crore people: Late T. K. Ramakrishna Circa 1946
About forty crore people live in our motherland ‘Bharata Bhoomi.’ Many of them have been haunted by the question, “Is it possible to provide khadi for all the forty crore people of our country?” Despite the many mills in existence in the country, the textile production capacity does not fulfill the needs of our people and such being the situation, the obvious question in the mind of common man is whether mere hand-spinning and hand- weaving is able to cater to the demand. Further, it is natural to ask: What is khadi’s relevance and stature in the present world? What are its basic principles? We should examine these aspects in the right perspective one by one.
Before World War II, it was estimated that the quantity of cloth produced per person in the country was just about twenty yards and apart from domestic production, clothes worth sixty crore rupees were supplied from outside. How do we bridge the deficit by spinning charaka and weaving in handlooms and be self-reliant with it was food for thought. In the year 1940, prior to World War II, there were one crore handlooms in the country. As a consequence of the war, many mills stopped producing textiles for the common man for over five years. Indeed, clothes to fulfill needs of military personnel gained precedence and were produced abundantly.
Further, in the wartime years of 1940-42, the number of handlooms also reduced for the reason that the cost of clothes had escalated significantly and the supply of yarn coming out of mills decreased somewhat. Additionally, market conditions were exploited by unscrupulous businessmen to their advantage by hoarding yarn to create scarcity that had a cascading effect on the prices of essential clothes. People experienced immense difficulties without actually being aware of the ill effects of war.
The situation eased a bit with the intervention of the government. Over a few years later the number of handlooms gradually increased to about 1.5 crores, partially also due to decrease in industrial textile mills resulting in an overall increase in handwoven cloth. Even so its progress was diminished as it became difficult to source sufficient yarn. The prices of clothes continued to remain high. This made us think how to improve the helpless situation in the post-war years.
When Sabaramati Ashram was opened by Gandhiji in 1918, yarn was used to be bought locally and khadi clothes were produced in the ashram although the difficulty in getting yarn locally quite persisted due to invasion from vested interests. Knowing fully well of this circumstance the only option then was to get hanji (sliver) from the mills and spin yarn with charaka by hand. Realising the danger in excessive dependence on mill owners Gandhiji got even the hanji done in the ashram itself. As an offshoot of all these turn of events, the Akhila Bharata Charaka Sangha came into existence with its initial capital of forty lakhs.
Over the years, Akhila Bharata Charaka Sanghas provided employment opportunities to about 4.5 crore people in about fifty thousand villages across the country. Wages to the extent of seven crore rupees were distributed. There is not a single cooperative institution in the world that provided employment at such a scale. We need to encourage such institutions in India as our country is not as economically strong as England. We have to provide more employment with least capital investment. Unlike America, we are a country with large human capital and therefore our dependence on machines could be minimal. In the circumstances as ours, unemployment due to mechanisation of textile production is dangerous for it robs of an opportunity to keep people employed and help sustainable living with other essential things.
Our country’s total requirement of cloth is about 800 crore yards. It is not difficult for a weaver to weave 800 yards a year. This translates to a requirement of one crore handloom weavers to fulfill the country’s needs. Now we do have as much handlooms but there is still a need to increase them. Secondly, around 55 lakh bales of cotton is required to produce as much cloth. India’s production volume of cotton currently is about 60 lakh bales. Therefore, we are self-sufficient with respect to cotton production.
Let us examine how we are positioned in spinning. For the targeted quantity of cloth, about 3,200 crore spun yarn is required. At about two hours a hank to spin a total of 6,400 crore hours would be required in a year. That amounts to about 20 crore man hours a day. Therefore, theoretically it is just sufficient if everyone in the country commits to spin for half-an-hour. Assuming that out of the whole population of about 40 crores, there are 11 crore farmers and about five crore people are involved in other forms of employment. Farmers typically have no agricultural activity for about three months a year. Should they all be able to contribute to spinning at two hours per day, the nation already gets about 22 crore man hours of spinning effort.
Further, realistically assuming that of the remaining population, about half of them contribute to spinning at one hour per day we would end up having an additional effort of 12 crore man hours. Going by an extra margin to about 32 crore man hours a day instead of twenty crore, we are still comfortably placed with 44 crore man hours to produce the desired quantity of cloth and by doing so khadi can be supplied to whole of India. By spinning for about half-an-hour a day and making clothes ourselves, we would save at least Rs. 20 from what would have otherwise been expended.
During the pre-war period, China was importing cloth from Japan that has stopped now. Due to scarcity of cloth, China is following the Indian model. In fact, it is interesting to note that the Chinese have named their looms the Gandhi Loom. “Khadi is not a symbol of slavery but a symbol of Swaraj,” the truth that Gandhiji spelled should be understood well by people. In order to maintain peace and harmony in our country we must be self-sufficient in all respects. The present ad hoc government is moving in this direction. As an example, let us consider the Madras province khadi industry that has been setup in twenty five hoblis (village clusters) at a cost of three crores. In a year or two, most textile mills will be out of business or there’s a chance that people will themselves reject machine-produced cloth. This is what will lead to Village Republic as Gandhiji has propounded. Our government should achieve all these objectives in totality.
2nd October 1946 Bapu’s 78th Birthday
[T. R. Dwarakanath can be contacted on Mob: 9448363395]
source: http://www.starofmysore.com / Star of Mysore / Home> Feature Articles / Friday – October 02nd, 2015